Well I dropped the Tera60 off with Darrell at KNA for some refreshing. The pinion nut had backed off, which in turn toasted the pinion bearing, and pinion seal.
I got a call from Darrell a few days later with an update. The drivers side carrier bearing showed signs of wear so it was replaced. I guess on the 60's the ring gear is spaced so far to one side, the torque has a tendency to wear drivers side carrier bearings faster. Interesting.
Darrell also discovered why the pinion nut had backed off. At some point in this axles life, the pinion was hammered into the housing, which knurled the end threads on the pinion shaft. So when the pinion nut was impacted on it stripped the threads enough to back off over time. Rather than scrap the gear set, Darrell chopped the boogered threads off the pinion shaft. This means the pinion nut is a few threads short of engaging the lock nut, but he thread locked the nut real good and torqued to spec. I don't see this being an issue, but it's something I'll mark and routinely check.
Lastly, the oil slingers were oriented wrong. Oil slingers are placed on the pinion shaft to keep oil on the pinion bearings to prevent them from running dry from take off, and to sling oil onto the bearings during use. In the case of my 60, the slinger was actually wearing down releasing metal shavings in the oil. This is likely what caused the pitting in the pinion bearings. So Darrell made the decision to just do a complete bearing overhaul, new pinion and carrier bearings.
Preload and backlash feel right, and no more end play in the pinion.
I got a call from Darrell a few days later with an update. The drivers side carrier bearing showed signs of wear so it was replaced. I guess on the 60's the ring gear is spaced so far to one side, the torque has a tendency to wear drivers side carrier bearings faster. Interesting.
Darrell also discovered why the pinion nut had backed off. At some point in this axles life, the pinion was hammered into the housing, which knurled the end threads on the pinion shaft. So when the pinion nut was impacted on it stripped the threads enough to back off over time. Rather than scrap the gear set, Darrell chopped the boogered threads off the pinion shaft. This means the pinion nut is a few threads short of engaging the lock nut, but he thread locked the nut real good and torqued to spec. I don't see this being an issue, but it's something I'll mark and routinely check.
Lastly, the oil slingers were oriented wrong. Oil slingers are placed on the pinion shaft to keep oil on the pinion bearings to prevent them from running dry from take off, and to sling oil onto the bearings during use. In the case of my 60, the slinger was actually wearing down releasing metal shavings in the oil. This is likely what caused the pitting in the pinion bearings. So Darrell made the decision to just do a complete bearing overhaul, new pinion and carrier bearings.
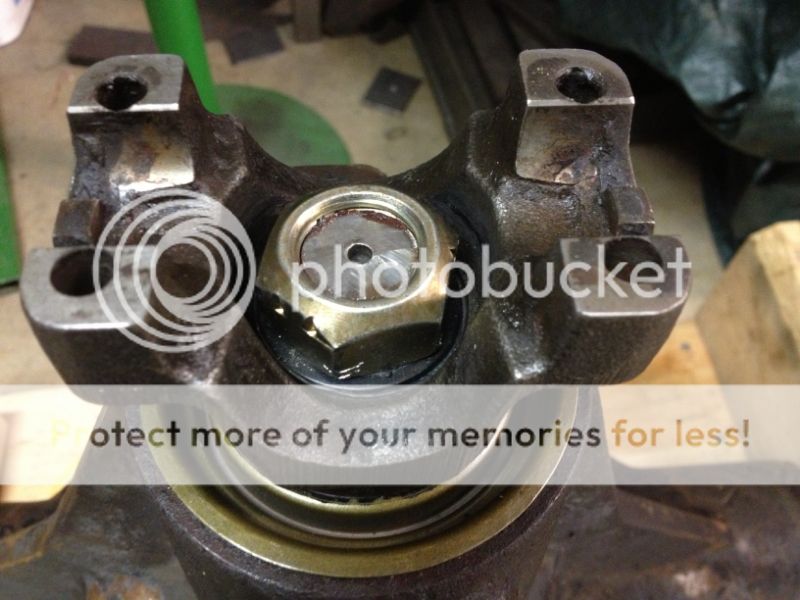
Preload and backlash feel right, and no more end play in the pinion.
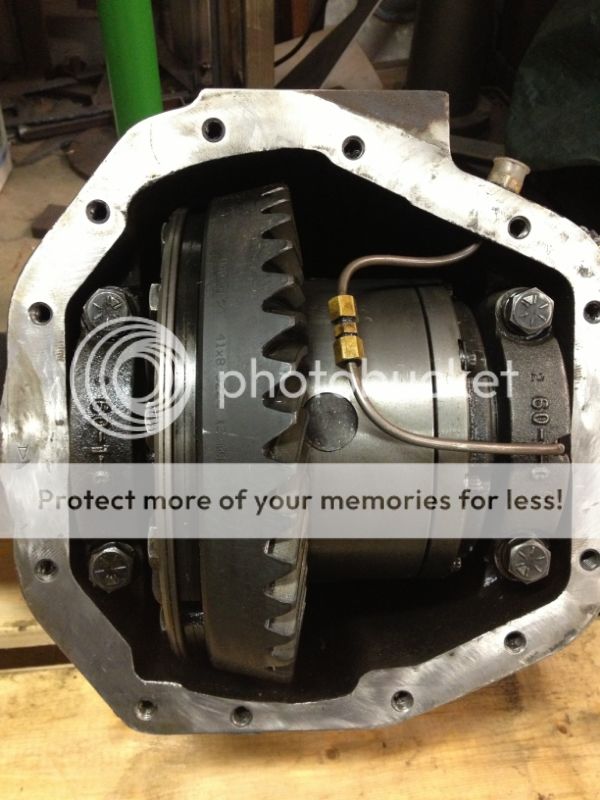