Lucas
NAXJA Forum User
- Location
- ZOO YORK CITY
Holy Hell this past week has been busy! Try finishing a 54 page thesis, building four axles, trying to swap them using a new suspension design, moving out, saying bye to all your friends and buring the proper bridges, applying for scholarships, AND try to move to NYC all at the same time...enough bitchin' though, time for some pics.
First, went to the steel shop to pick up some plate/tube. 22 feet of 1.5od .25" wall tube. This stuff was WAAAAAAY beefier than I had expected. I think when I get to steering it will be practically unbendable. Cut some up and stuck it on the end of the radius arms:
Those are big RE joints. The problem withth the radius arms are that the factory studs are a little less than 7/8". My tube has a 1"id, so there was a lot of play. I didn't want to trust a single weld between the arm and the tube, so I welded material onto the factory studs, turned down the weld blob until it was uniform, then pressed the plug into the tube. No pics because I suck, but it was pretty tech I think.
that night I finished around 2am, went to a party and drank too much too quickly, and walked face first at full speed into a glass door:
this was after I cleaned up. Tip of the day= drunk college girls think idiots walking into doors are adorable
Anyway, loaded up 4 38"s and my 4 35"s and rims and went to the shop to get them mounted:
#$#$#y^%$in' tire shop chunked rubber ouut of one of my 35s on the machine. I didn't find out until much later though. No time to correct it now though
First, went to the steel shop to pick up some plate/tube. 22 feet of 1.5od .25" wall tube. This stuff was WAAAAAAY beefier than I had expected. I think when I get to steering it will be practically unbendable. Cut some up and stuck it on the end of the radius arms:
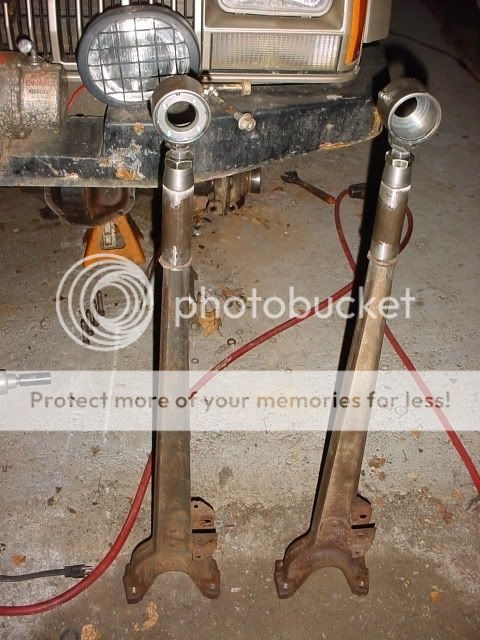
Those are big RE joints. The problem withth the radius arms are that the factory studs are a little less than 7/8". My tube has a 1"id, so there was a lot of play. I didn't want to trust a single weld between the arm and the tube, so I welded material onto the factory studs, turned down the weld blob until it was uniform, then pressed the plug into the tube. No pics because I suck, but it was pretty tech I think.
that night I finished around 2am, went to a party and drank too much too quickly, and walked face first at full speed into a glass door:
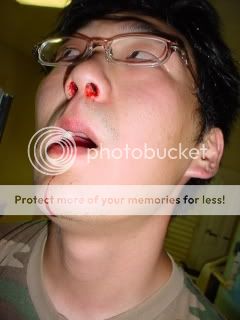
this was after I cleaned up. Tip of the day= drunk college girls think idiots walking into doors are adorable

Anyway, loaded up 4 38"s and my 4 35"s and rims and went to the shop to get them mounted:
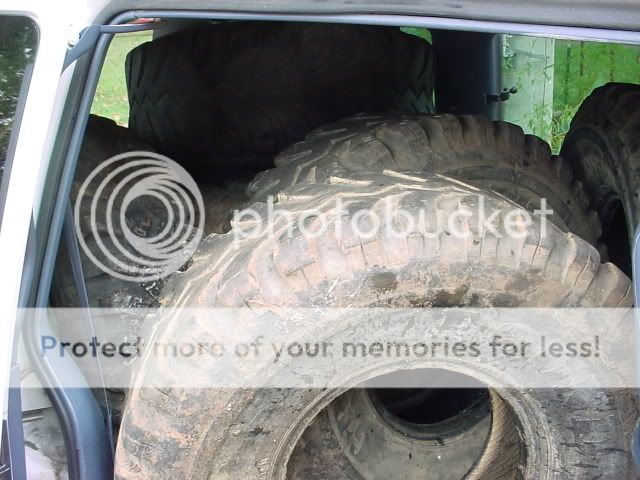
#$#$#y^%$in' tire shop chunked rubber ouut of one of my 35s on the machine. I didn't find out until much later though. No time to correct it now though

Last edited: