- Location
- In a strange land
Preamble: This is going to be a long post with a whole bunch of pictures. One reason for the level of detail is so that anyone who would like a set of these can evaluate the option for themselves. This took me about seven months from receipt of armor to final installation. I am not a professional with a bunch of specialized tools. If you can weld then you can probably do this. Note that I am also including my mistakes so that hopefully someone else can learn from them. At the very least it will help me remember not to make them again. I hope.
A big part of the purpose of this thread is to help with reasonable expectations, not to bash anyone’s product. You will note I had some challenges fitting these. I suspect everyone who tries to fit armor on an XJ runs into some challenges. Among other things, the XJ platform covered a span of 18 years and two manufacturers. Neither of those manufacturers have been particularly noted for their ability to maintain world class quality control. I have been involved in manufacturing aftermarket products and I know that dealing with someone else’s tolerances and seemingly random design variations is no small challenge. I am simply grateful for the aftermarket support which I enjoy as an owner of an XJ. It sure beats having to fabricate components from scratch.
I know I am not the only person to purchase something like this and then wind up putting it in a corner of the garage and glaring at it for a few months. I am hoping that by providing the details of my walk through this project I will help others be prepared to deal with the challenges so they can keep moving forward to the end and get there more quickly than I did.
Now, on to the write-up.
This project got bumped up in the priority list when I found out just how bad the reverse lights are on my ’96 XJ. The first winter of owning my Jeep I didn’t drive it in the evening because the headlights would randomly go out as if this were a British car with Lucas components. Some relays and bits from Daniel Stearn took care of that. But the next winter I found out that the reverse lights are completely useless when it comes to illuminating the area behind you. Perhaps they will alert an attentive driver to your intentions of backing up…perhaps…but they are a sad excuse for a light.
[FONT="]Now that I have gone down this route I think I would have been wise to look into the Oldsmobile Aurora mod, but that tends to preclude the use of a bumper mounted spare tire, and I am not yet ready to give up that option. And I understand that mod requires cutting some holes in the fiberglass hatch. Besides, I like the idea of custom tail lights. I really became committed to the idea when I saw this thread:
http://www.naxja.org/forum/showthread.php?t=1110092
[/FONT] Then it became a question of how to come up with the housings. I could follow the path of the OP in that thread and make my own metal housings, but then I considered the potential risk of something hitting the tail lights and rather than just busting up the tail lights instead transferring the damage to the quarter panels. Quarter panel armor seemed like a good idea, but how to go about getting the rectangular LEDs? Everything I had seen on the market was set up for a pair of 4” round LEDs. I really did not want to try to fill in the existing holes and start all over, but that was looking like my best option.
[FONT="]Then I found that Ares Fabrication offer the option of armor with blank light boxes. That was exactly what I needed.
http://aresfabrication.com/?page_id=662
[/FONT] (Note they also make armor for two door XJs. I have seen a number of threads where folks were lamenting the lack of armor for two doors.)
I ordered them in early January and received them in early February. These were a custom order. I expected to wait a bit for them. I still got antsy about getting them, but the time was not unreasonable.
Once I got them and some rectangular LEDs I set to work laying things out. Guess what? Rectangular LEDs are all over the map when it comes to dimensions. I am sure there is some limit on tolerances, but those big rubber grommets seem to forgive a lot of variance. I knew what I wanted to run for reverse lights, but finding a brake/tail light to match was a roll of the dice. My first choice was a no-go. Fortunately the second set I tried was pretty close.
I set to work laying things out with my sophisticated CAD system.
I then transferred my patterns onto the blank tail light boxes. I first traced with a Sharpie, then widened the Sharpie tracing, then again traced, but this time with a scribe tool. That gave me a nice fine line with good contrast.
I clamped both pieces of armor to a sawhorse.
I then used a 4 ½” angle grinder with a cut-off wheel to plunge cut along the inside edges of the straight lines.
I then used a jigsaw with a metal cutting blade and lots of wax from a nixxstick in order to make the curved cuts. I left just the smallest bit of material at each corner for the sake of stability until I had made my way around the fourth corner on each opening.
Then it was just a matter of removing the little tabs to drop out the center.
By the late afternoon I had this:
[FONT="]From there it was a whole lot of grinding and filing to sneak up on the final dimensions. I probably spent about two hours per opening. The entire time I was thinking how much easier this would be if done on a plasma CNC. The closer you can cut to your final line without going beyond it the less effort required to achieve a final fit.[/FONT]
A big part of the purpose of this thread is to help with reasonable expectations, not to bash anyone’s product. You will note I had some challenges fitting these. I suspect everyone who tries to fit armor on an XJ runs into some challenges. Among other things, the XJ platform covered a span of 18 years and two manufacturers. Neither of those manufacturers have been particularly noted for their ability to maintain world class quality control. I have been involved in manufacturing aftermarket products and I know that dealing with someone else’s tolerances and seemingly random design variations is no small challenge. I am simply grateful for the aftermarket support which I enjoy as an owner of an XJ. It sure beats having to fabricate components from scratch.
I know I am not the only person to purchase something like this and then wind up putting it in a corner of the garage and glaring at it for a few months. I am hoping that by providing the details of my walk through this project I will help others be prepared to deal with the challenges so they can keep moving forward to the end and get there more quickly than I did.
Now, on to the write-up.
This project got bumped up in the priority list when I found out just how bad the reverse lights are on my ’96 XJ. The first winter of owning my Jeep I didn’t drive it in the evening because the headlights would randomly go out as if this were a British car with Lucas components. Some relays and bits from Daniel Stearn took care of that. But the next winter I found out that the reverse lights are completely useless when it comes to illuminating the area behind you. Perhaps they will alert an attentive driver to your intentions of backing up…perhaps…but they are a sad excuse for a light.
[FONT="]Now that I have gone down this route I think I would have been wise to look into the Oldsmobile Aurora mod, but that tends to preclude the use of a bumper mounted spare tire, and I am not yet ready to give up that option. And I understand that mod requires cutting some holes in the fiberglass hatch. Besides, I like the idea of custom tail lights. I really became committed to the idea when I saw this thread:
http://www.naxja.org/forum/showthread.php?t=1110092
[/FONT] Then it became a question of how to come up with the housings. I could follow the path of the OP in that thread and make my own metal housings, but then I considered the potential risk of something hitting the tail lights and rather than just busting up the tail lights instead transferring the damage to the quarter panels. Quarter panel armor seemed like a good idea, but how to go about getting the rectangular LEDs? Everything I had seen on the market was set up for a pair of 4” round LEDs. I really did not want to try to fill in the existing holes and start all over, but that was looking like my best option.
[FONT="]Then I found that Ares Fabrication offer the option of armor with blank light boxes. That was exactly what I needed.
http://aresfabrication.com/?page_id=662
[/FONT] (Note they also make armor for two door XJs. I have seen a number of threads where folks were lamenting the lack of armor for two doors.)
I ordered them in early January and received them in early February. These were a custom order. I expected to wait a bit for them. I still got antsy about getting them, but the time was not unreasonable.
Once I got them and some rectangular LEDs I set to work laying things out. Guess what? Rectangular LEDs are all over the map when it comes to dimensions. I am sure there is some limit on tolerances, but those big rubber grommets seem to forgive a lot of variance. I knew what I wanted to run for reverse lights, but finding a brake/tail light to match was a roll of the dice. My first choice was a no-go. Fortunately the second set I tried was pretty close.
I set to work laying things out with my sophisticated CAD system.
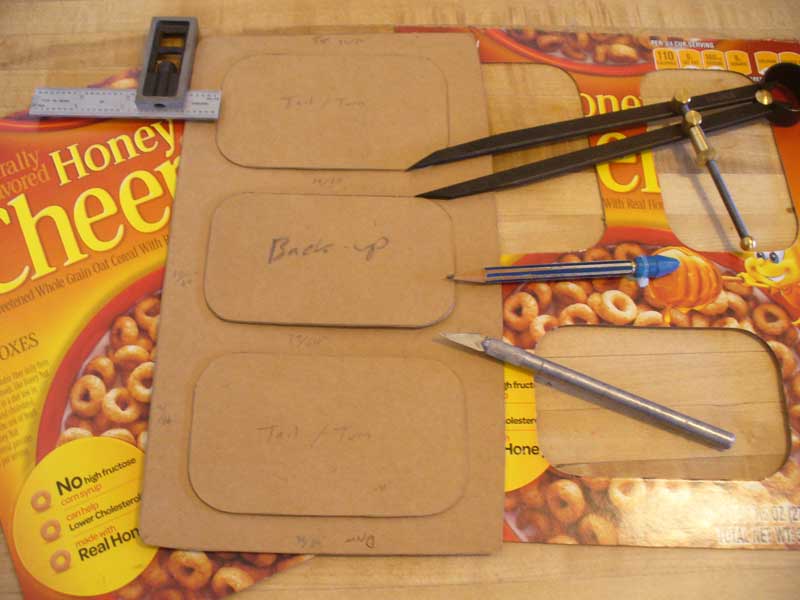
I then transferred my patterns onto the blank tail light boxes. I first traced with a Sharpie, then widened the Sharpie tracing, then again traced, but this time with a scribe tool. That gave me a nice fine line with good contrast.
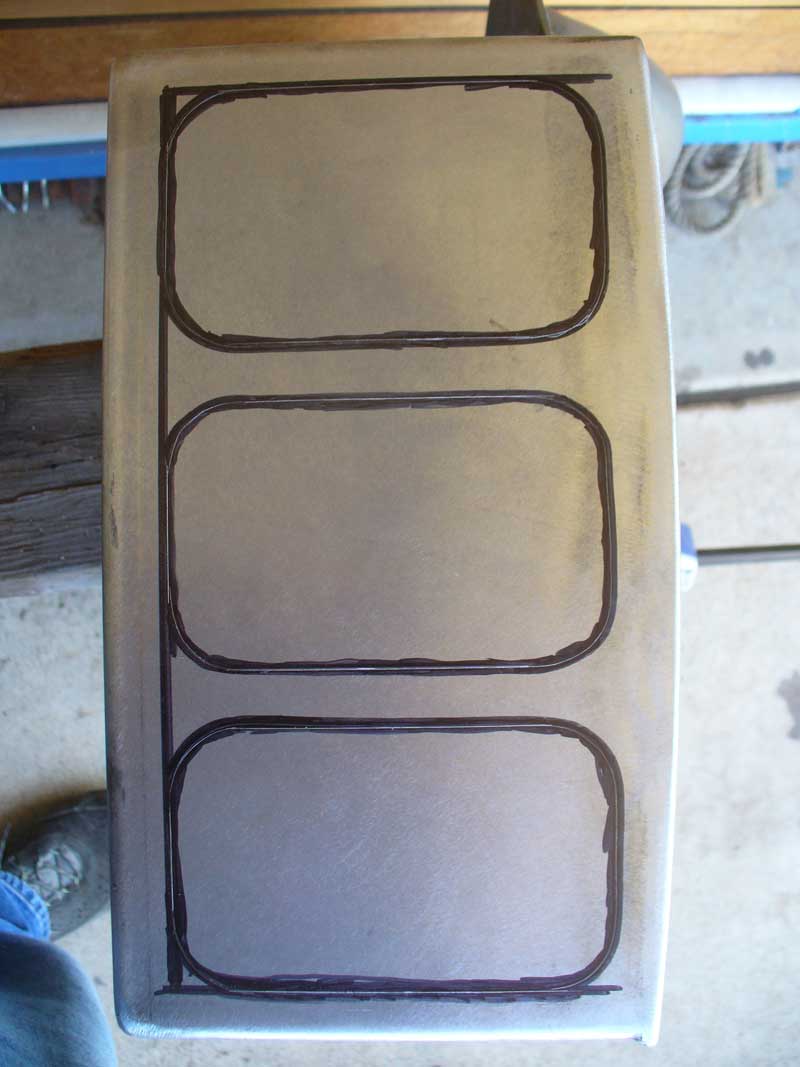
I clamped both pieces of armor to a sawhorse.
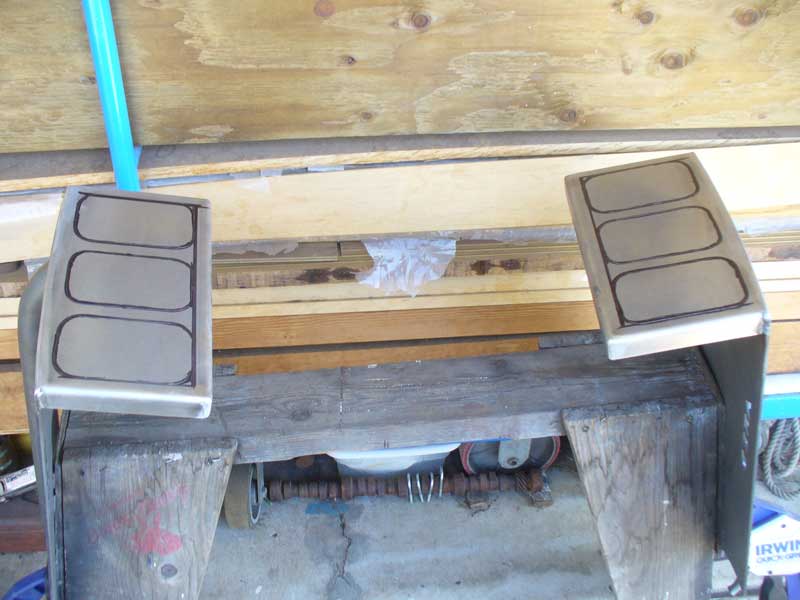
I then used a 4 ½” angle grinder with a cut-off wheel to plunge cut along the inside edges of the straight lines.
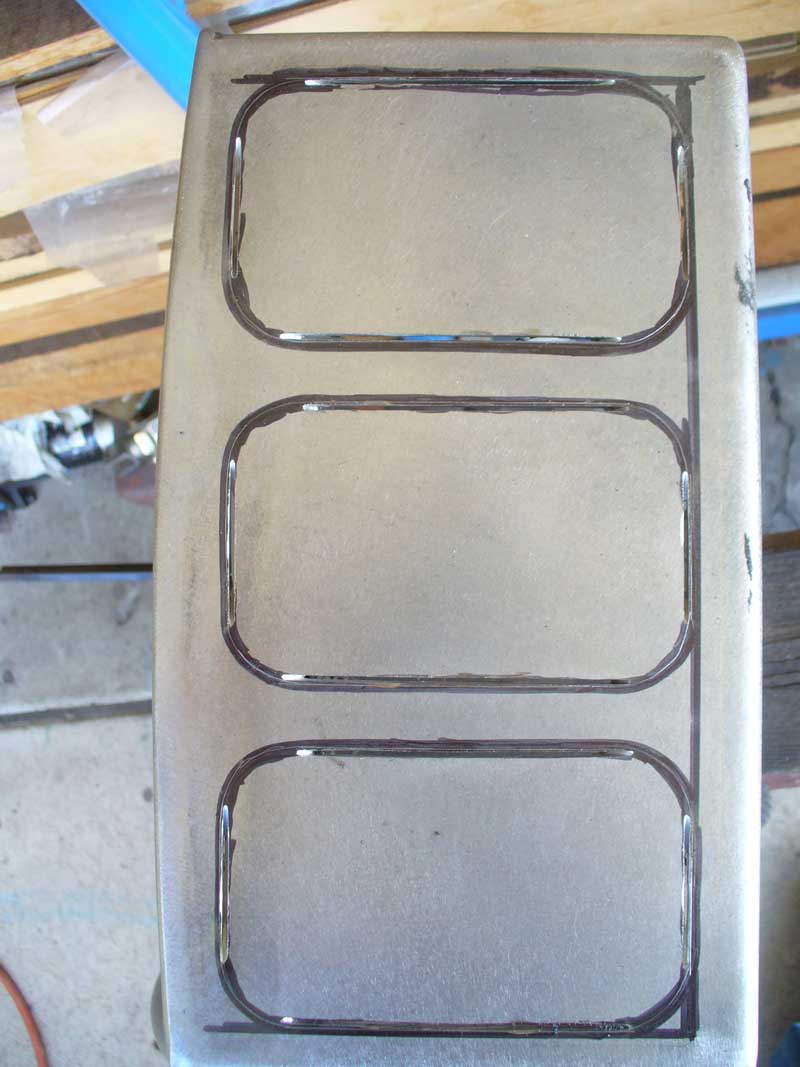
I then used a jigsaw with a metal cutting blade and lots of wax from a nixxstick in order to make the curved cuts. I left just the smallest bit of material at each corner for the sake of stability until I had made my way around the fourth corner on each opening.
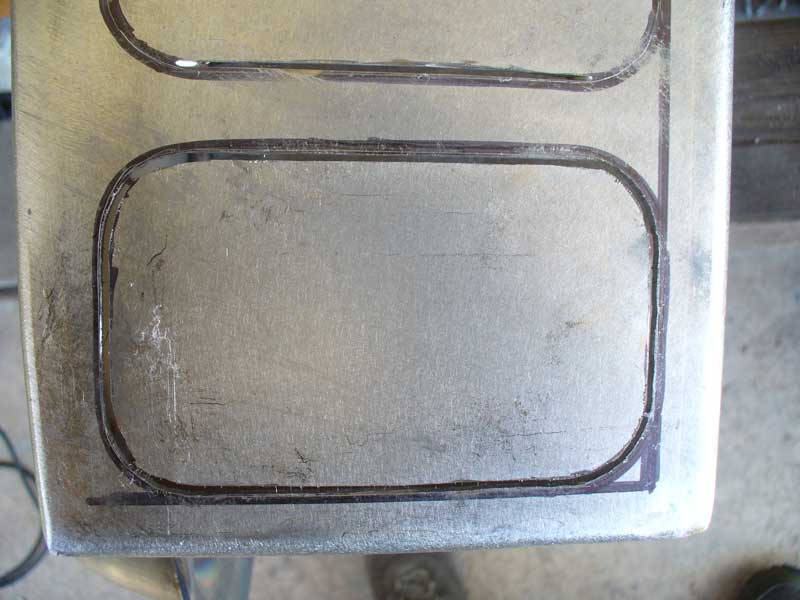
Then it was just a matter of removing the little tabs to drop out the center.
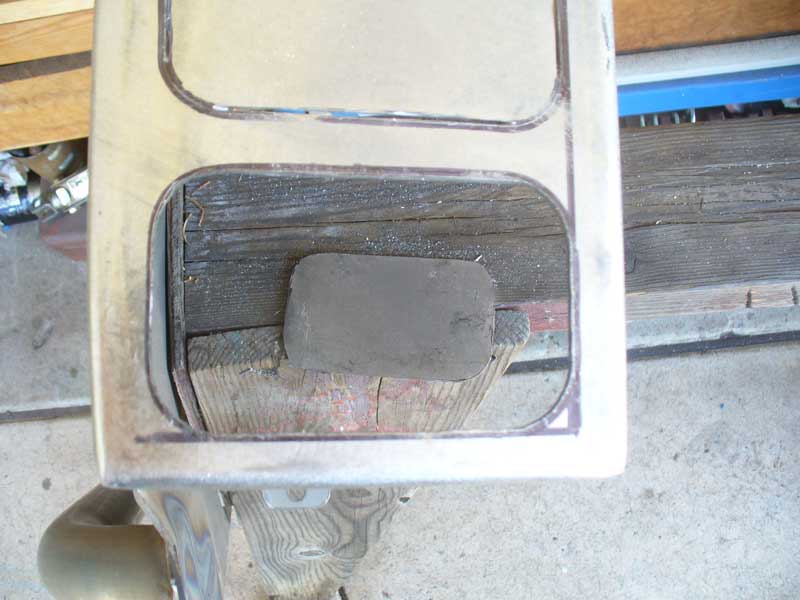
By the late afternoon I had this:
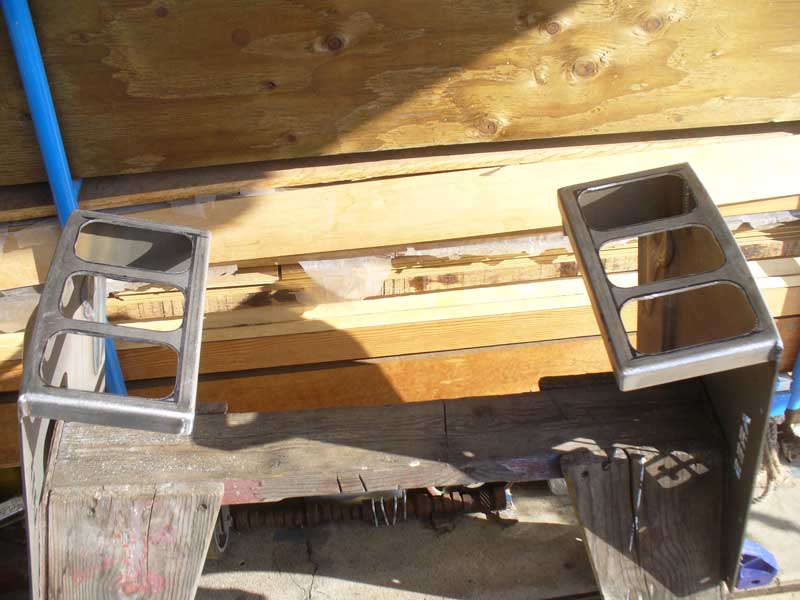
[FONT="]From there it was a whole lot of grinding and filing to sneak up on the final dimensions. I probably spent about two hours per opening. The entire time I was thinking how much easier this would be if done on a plasma CNC. The closer you can cut to your final line without going beyond it the less effort required to achieve a final fit.[/FONT]